製造業と言えば生産管理システムですね、私たちの会社でも使っています。
ところで生産管理ってなんでしょうか?改めて聞かれるとわかないものです。
この記事は生産管理業務についてまとめました。
生産管理業務の全体のイメージや個別の業務の内容を説明しています。
これから製造業に就職や転職される方には仕事の内容をイメージできて良いかと思います。
また、若手教育や新入社員教育において生産管理業務の説明で悩んでいる方には参考資料になるかと思います。
生産管理の基本
生産管理とは?
製品の需要予測や販売計画から生産計画を作成し、それに基づいた原材料の調達、人員の配置、生産の実施など、 ものづくりの流れをコントロールする、総合的な管理活動のことを生産管理といいます。
生産管理の目的
ものづくりの原点は、品質(Quality:よいものを)、コスト(Cost:より安く)、納期(Delivary:より短期間で)追求し続けることにあります。
製品をお客様に届けるまでには、多くの人により様々な業務が行われます。
それぞれが場当たり的に行われていては、多くの無駄が発生します。
生産管理業務の目的は、様々な絡み合った業務を統制することで、QCDを最適化して企業の競争力を高めることです。
Q・C・Dについて
Q(Quality)
Qは品質のことです。
製品が長持ちするような「丈夫さ」がまず思いつくかもしれませんが、「使いやすい」「人に優しい」「機能が素晴らしい」といった事も機能の一部です。
C(COST)
Cは原価のことで、工場では材料費や人件費、設備投資などが主な要素です。
D(Delivery)
Dは納期、あるいは配送ですが、実は期日だけでなく納品数も一緒に考えなくてはいけません。
そのため、このDを「量・納期管理」と呼ぶこともあります。
QCDはトレードオフの関係にあります。
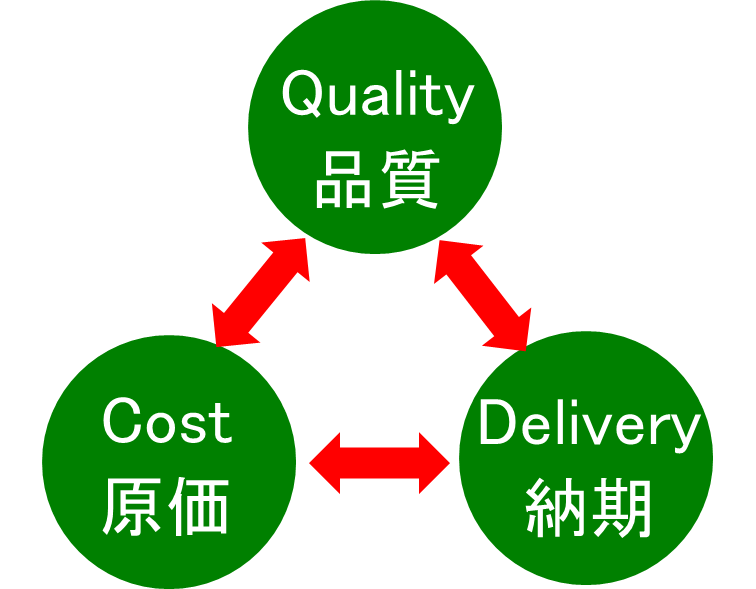
例えば不良品を出さないために入念なテストを繰り返すのは品質面では良いですが、時間がかかって納期が間に合わなくなったり、人件費が余計にかかったりしては何もなりません。
QCDをバランスよく最適化する事がものづくりの基本であり、生産管理業務の役割と言えます。
生産管理の仕事の内容
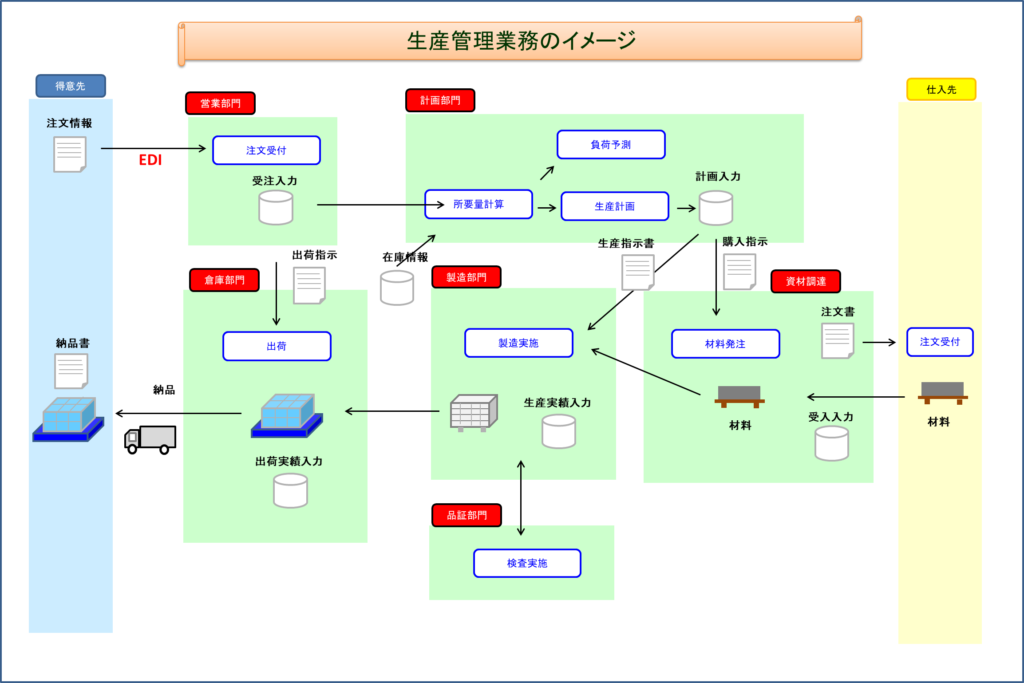
生産管理の仕事それぞれの企業により異なります、ここで説明する内容は私が勤める工業での事例になります。
受注管理
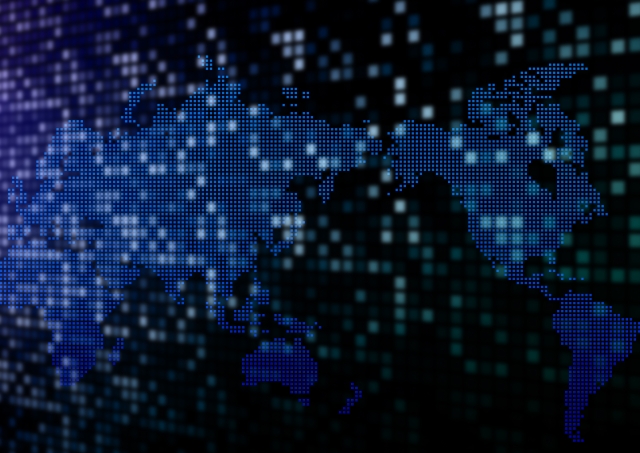
注文受付・受注データ入力
主に営業部門が管轄する業務です。 お客様からの注文を受け付けて製品番号や納期、数量などの注文情報を、受注データとしてデータベースに保存します。 注文データの種類は確定注文と内示注文があります。 保存したデータは売上予測の計算や生産計画作成、負荷計算、出荷管理などの基礎データとして使われます。 また、客先の注文情報はインターネットで受け渡しが行われて、システムを通じてデータベースに取り込む方法が一般的です。
追加注文や増産の対応
顧客注文の動向を的確に把握し、通常と違う場合は客先からの情報収集や、社内の情報伝達、指示を迅速に行う必要があります。 例えば急な注文においては調達部門へ材料の追加手配、計画部門へは計画変更を指示します。
客先の注文が先々大きく増える場合には各部門と素早く調整を行わないと、原材料や購入部品の調達、作業者の増員など、 準備が間に合わなくなり、客先納期を守れなくなるばかりでなく、製造部門やその他の多くの部門で無駄作業を発生させてしまいます。
量産終了時の対応
量産終了時は注意が必要で、きちんと生産数を合わせないと売れない製品を作ってしまう事になります。 量産終了のタイミングを的確に捉えて社内に伝達する事は重要な仕事です。
生産計画
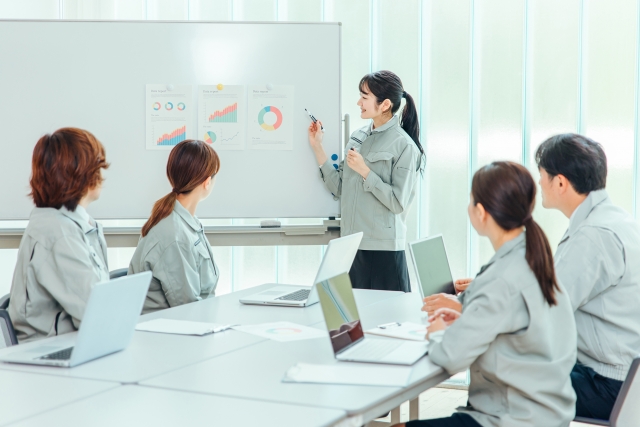
営業部門で受け付けた注文情報は計画部門により生産計画の作成、材料の調達指示、生産指示が行われます。 生産計画は注文情報、部品個々の在庫数量から何を、何個、いつまでに作るのかを決めた上で、日々の作業量を平準化する事で作成されます。
所要量計算
「何を、何個、いつまでに作るのか」、それを決めるには注文数から在庫をマイナスした必要数を計算して、 場合によっては生産ロット数にまるめる、最小ロット数や最大ロット数を考慮して数量を決めます。 また、客先の納期から加工日数を考慮した日が生産日になります。 このような計算の仕組みを所要量計算(MRP)と呼びます。
所要量計算の作業は膨大な作業工数になります、通常ではコンピューターのシステムを使って行います。 また、所要量計算には在庫情報が正確に維持されることが前提になります。 在庫情報は製造部門での生産実績、資材部門での購入実績、倉庫部門での出荷実績など、 それぞれのデータ入力で維持されています。
所要量計算で得られた結果は社内の生産ライン向けには生産指示データとして生産計画作成の基礎データになり、 仕入先向けには発注データとして資材調達の基礎データになります。
負荷予測
製品の販売予測や受注データや計画データから所要量を算出し、生産に必要な人員や設備の仕事量を予測したものを負荷予測といいます。 計算期間は長期、中期、短期に分けた情報を必要に応じて計算します。
- 長期 半期ごと(年2回)
- 中期 毎月
- 短期 毎週
仕事量の算出は『 仕事量 = 生産個数×1個あたりの生産時間 』を全製品積み上げることで計算出来ます。
負荷予測資料は収支予測で必要な人件費の計算にも使われ、キャパシティーと比較することで人員配置や残業時間、増員等の検討が可能になります。
生産計画作成
所要量計算から得られた結果が生産計画になりますが、機械的に行われた所要量計算の計算結果は、 それぞれの生産ラインが保有する生産能力や、日々の仕事量のばらつきを考慮していません。 製造部門での手空きや残業の発生をできるだけ出さないように、生産計画は日々の仕事量を均等にする必要があります。 日々の作業量を平準化しする作業を「負荷平準化」や「山崩し」と呼びます。 その作業は計画担当者にて手作業で行われます。 山崩しにより生産能力に合わせて実行可能な生産計画を作成することを負荷計画とも呼びます。
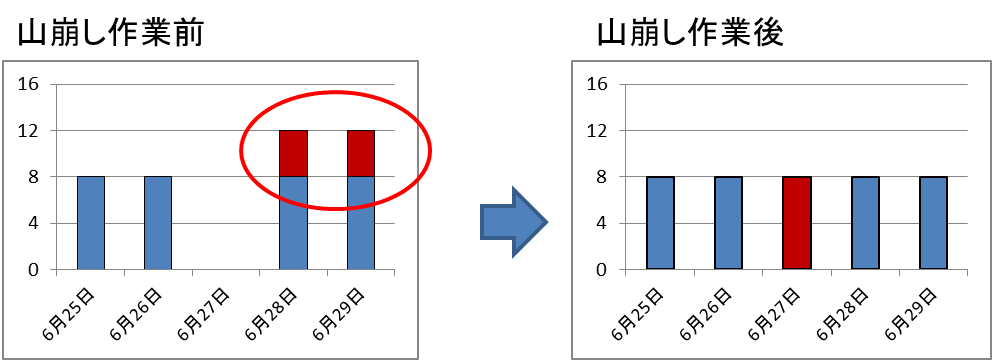
生産計画作成において視覚的に操作がしやすい、自動化が可能などの「生産スケジューラー」というパッケージソフトもあります。
資材調達
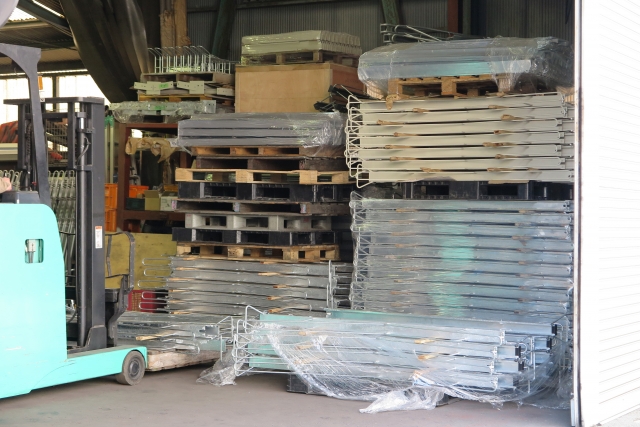
生産計画に基づいて、生産で使用する原材料、購入部品などの資材の調達を行います。 無駄な購入を行わないように納期、数量を計画に合わせてタイミング良く調達します。 また、原材料以外に外作加工業者の管理も資材部門の管轄になります。
納期管理
納期通りに納品が行われるように仕入先と連絡をとり、納期遅れや数量不足等の問題が発生した場合には、 社内の各部門と調整をとります。 作業の方法としては発注一覧表のリストから納入予定を把握して問題がありそうなものをチェックして行きます。 前工程の生産遅れなどで急ぎでの手配が必要なものは十分に注意を行う必要があります。 また、客祭の注文の取り消しや後ずらしが発生した場合に、可能であれば納入を調整してもらいます。
受入処理
調達した品物は品番や数量などを伝票と照合し問題がなければ定められた場所に保管します。 また伝票はお金と同じなので紛失などしないように十分注意します。 システムで生産管理を行っている場合は受入情報を入力します。それにより在庫情報の更新が行われます。 また、買掛金のシステムと連動しているシステムであれば仕入れ金額の情報が同時に作成されます。
仕入先在庫管理
加工業者へは原材料や仕掛り部材を支給する場合があります。 その場合は支給した部品を把握する必要があるため、支給実績や受入実績の記録を取り、 加工業者で保管されている理論在庫を把握していなければいけません。 生産管理のシステムによっては支給及び受入の実績から自動的に預け在庫の算出が可能です。 また部材の支給には有償と無償が有り、無償の場合は自社の資産になるので必ず管理しなければいけません。
購入金額管理
購入金額の管理は資材部門の重要な役割です。 必要以上に購入を行いように期別や月別等で予算を設定して、その金額を超えないように管理します。
仕入先品質管理
仕入先の品質管理の資材部門の管轄になります。 不良が発見された場合は仕入先に連絡をとり、返品や代替え納入、選別などの手配をとります。
製造実施
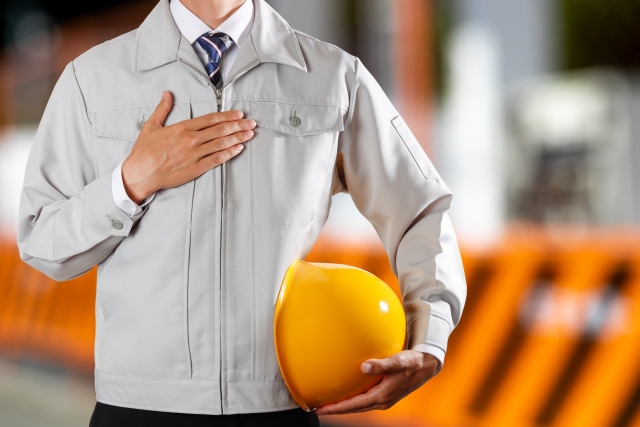
生産指示
計画部門で作成された生産計画から日々の生産が行えるように、製造部門に対して生産指示を発行します。 生産指示に基づいて製造部門は生産を行います。 計画部門から出される生産指示をそのまま生産する場合と、生産指示を製造部門の管理者やライン長等がアレンジして生産順序を決める場合があります。 人員配置、設備配置など現場の状況で生産計画の実行可否が流動的な企業においては現場でアレンジするケースが多くなります。
生産実績入力
システムで生産管理を行っている場合は生産結果をデータとして入力します。 部品番号、生産日、生産数、不良数などが対象です。 生産実績を入力した結果により在庫情報が更新されます。 入力の間違いは在庫を狂わせて納期の遅れや過剰在庫の原因となり、大きな損失につながります。 正確なデータ入力が必要です。 また、入力は生産終了後できるだけ早く行わなければいけません。
製造部門はものづくりを実施する部門であり、製造業では企業の中心になる部門です。 そのために管理項目も多く、例としては生産性の評価資料や不良数、不良金額の集計、品質状況などがあります。 それらに必要な情報も生産後に記録します。 また、生産時間の情報など生産計画立案の基礎情報として必要なものはフィードバックされて、計画精度の向上に役立てられます。
改善活動
いかに良いものを、安くつくるかも製造部門のテーマになります。 日々の生産活動を見ながら金型や治工具などの道具の改造や加工工程の変更などの改善活動を、 技術部門や品証部門と進めることも常に行っています。
品質管理
客先の要求する品質を維持するために品質保証部門が主観して品質管理を行います。 生産時に製造部門で行う工程内検査、製品が出来た時に行う受入検査、製品出荷時に行う出荷検査により品質が確保されていることを確認します。 検査時は必ず検査結果を記録して、不良等の品質問題が発生した場合は履歴を追えるようにしておきます。 検査の実施は検査の基準を作成した「検査企画書」に基づいて行われます。
不良が出た場合の対応窓口や、社内への対応指示も品証部門にて行っています。 不良の発生状況は品証部門にて管理を行い、品質改善に役立てるように全部門へ働きかけます。
トレーサビリティー
トレーサビリティ(Traceability)とは、トレース(Trace 追跡)とアビリティ(Ability 能力)を組み合わせた造語で、日本語では「追跡可能性」と訳されます。 その製品がいつ、どこで作られたかを追跡出来るようにする仕組みのことを言います。 原材料の調達から生産、出荷までが企業内での対象範囲と考えられますが、 広義ではユーザーでの消費や廃棄までを追跡可能な状態にする事が求められます。
出荷管理
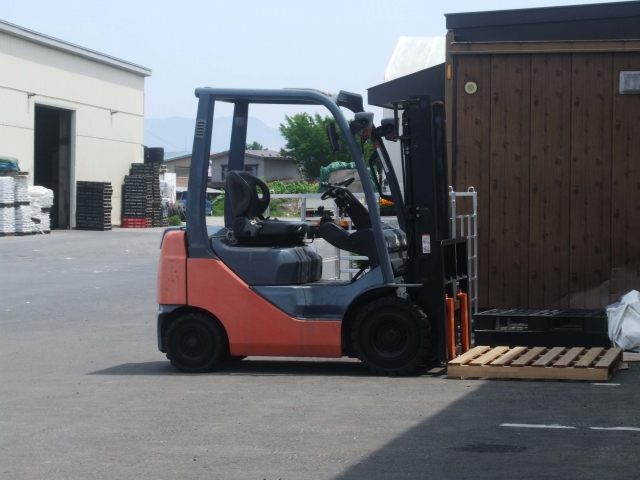
出荷指示
工場内で完成し検査で合格した完成品は倉庫で保管され、出荷の指示に基づいて出荷可能な状態に梱包して出荷します。 出荷の指示は営業部門から出荷管理部門へ指示されますが、指示された通りの製品、指示された通りの数量で出荷しなければいけません。 出荷すべき製品を間違えたり、数量を間違えると不良の扱いになります。またお客様にも迷惑をかける結果になります。
製品納期管理
製品の出荷においてはお客様の注文通りの製品、納期、数量で行われたか管理する必要があります。 生産の遅れ等で注文通りの出荷が行われない場合は、客先に連絡を取り遅延の可否を確認しておかないと迷惑をかけることになります。 遅延が頻繁に発生する場合は、製造部門や計画部門に問題定義する必要もあります。
輸送費
納品時の輸送においてコストをかけないことも重要です。
例えば同じ方面にある客先は納品のタイミングを同じ日にする。客先と交渉をして納品する日を週に一度にまとめるなどにより輸送費を削減することも必要です。
在庫管理
在庫管理は生産管理において最も重要な管理項目です。 通常は倉庫への入庫数と出庫数から在庫数をコンピュータシステムで管理します (生産管理システムでは生産実績入力と出荷入力が入出庫を兼ねている)。 継続的に維持管理されて生産計画にフィードバックされます。 それにより在庫があるものは手配されない、必要な数だけが手配される計画になります。
在庫は品目ごとに在庫単価が決まっていて金額の算出が行われます、企業の収支上で必要となる重要な項目です。
実地棚卸
何かの理由でシステム上の在庫数と実際の在庫数違ってくることがあります。 そのため月に一度や3ヶ月に一度などのサイクルで実際の在庫数を数えて、システム上の在庫を合わせる作業を行う事が一般的です。 実際の在庫を数える作業を実地棚卸や棚卸と呼びます。
在庫は少ないほうが良い?
在庫を持つことで売上機会を逃すことが少なくなるなどメリットもありますが、 在庫は数量においても金額においても少ないほうが良いとされます。 原材料をまとめて買えば安く買える、1回の生産数量を増やすことで段取り回数が減り生産効率は数字上ではあがると思われがちですが、 それにより物が増えて運搬の時間、物を探す時間など、目に見えない無駄が増える事が多いです。 サビの発生などの製品劣化のリスクもあります。 何よりも在庫を多く持つことは資金繰りを悪化させるという経営上でもデメリットにもつながります。
但し、極端な在庫の圧縮で生産性や購入価格を悪化させないように、バランス良く在庫数を管理することが必要です。